Better Hydro: labour and working conditions at Santo Antônio, Brazil
This case study is featured in Better Hydro: Compendium of Case Studies 2017, which highlights examples of good practice in hydropower sustainability across all aspects of project development. You can download the full compendium here.
Key project features
Project stage: implementation
Developer/operator: Santo Antônio Energia (SAE)
Capacity: 3,568 MW
Annual generation: 21,236 GWh
Reservoir area: a total of 422 km2 at full supply level, not including backwater effects, out of which 142 km2 is the original river
Head: 14.7 m
Purpose: power generation
Commissioning: 2012-2016
The Santo Antônio project required up to 20,700 workers during its construction phase, but faced strong competition for qualified labour in the region. This case study demonstrates how the project provided excellent worker satisfaction and retention.
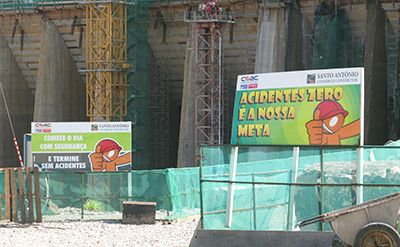
The Santo Antônio project is located on the Madeira river, 7 km upstream of the city of Porto Velho, the capital of Rondônia state in north-west Brazil. The Madeira river is a major tributary of the Amazon, the world’s largest river in terms of run-off volume.
The Santo Antônio project is designed to make maximum use of the water resource potential, with minimal negative impact on the Amazon region.
The project required a large number of workers – up to 20,700 in 2011.
However, other large hydropower projects being developed in the Amazon region, combined with a construction boom across various sectors, meant fierce competition for qualified labour. The potential consequences of this included higher staff turnover and upward pressure on salaries.
Construction on Santo Antônio began in September 2008, when the Brazilian Institute of Environment and Renewable Natural Resources (IBAMA) issued an installation licence. The dam was closed and reservoir filling began in September 2011, following IBAMA’s issue of the operational licence. The first two turbines became operational in 2012, but the plant was only completed only in 2016, following an extension that added additional capacity.
Santo Antônio Energia (SAE) appointed an engineering-procurement-contraction consortium for the construction of Santo Antônio. This consortium, Consórcio Construtor Santo Antônio (CCSA), consisted of three main components: a civil works consortium, Consórcio Santo Antônio Civil (CSAC), made up of Odebrecht (leader) and Andrade Gutierrez (both part-owners of the plant); an electro-mechanical equipment consortium, Grupo Industrial do Complexo Rio Madeira (GICOM), consisting of Alstom Power, Alstom Grid, Andritz, Bardella, Siemens and Voith; and Odebrecht, responsible for electro-mechanical installations. SAE, CCSA and CSAC all had designated human resources and HSE (health, safety and environment) managers.
The Acreditar programme was an important tool for the planning and supply of qualified staff for the project (please see page 88 for more details). Up until 2013, safety was proving to be a challenge at Santo Antônio. In response, CCSA established a set of targets on the reduction of accidents, comprising:
- 40 per cent reduction of accidents without absence
- 25 per cent reduction in lost time accidents
- 40 per cent reduction in cumulative days lost due to severe accidents
These targets were progressively on track for success throughout 2013 and 2014. For example, the rate of accidents without leave fell from 10.1 per million work hours in 2012 to 6.3 in 2013, and down to 4.6 in the first four months of 2014.
Lost time accidents (i.e. hours of lost working time) fell from 7.8 to 5.4 to 4.4 per million work hours, respectively, over the same period.
The project suffered a total of 10 fatalities (seven on site and three off site), but there have been no fatalities at the project since October 2013.
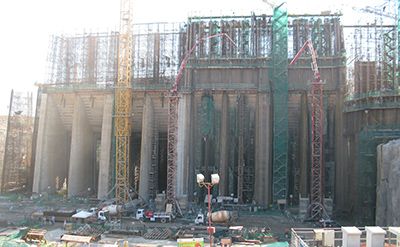
SAE and the consortium members focused intensively on workers’ needs and safety. They put in place systems for continuous monitoring and auditing by external parties. Implementation of safety requirements was delivered through a project-wide health, safety and environmental management system (SSTMA). The SSTMA standards applied to everyone, including sub-contractors. Each new contractor was given a risk assessment and constantly followed up and scored on performance.
The project’s policy was to focus on quality rather than cost when hiring staff. The workers’ facilities were world-class, offering good, healthy food, excellent and well-staffed medical facilities, air-conditioned lodging and plenty of clean showers and toilet facilities. Workers remarked that the leisure and social facilities were the 'best' they had ever experienced.
A specific programme for staff retention was put in place. This included a workers’ commission of representatives and an ombudsman system, through which workers could report grievances.
Risk-mapping and operational analysis provide a basis for specialised safety procedures
SAE initially assessed occupational safety risks on the construction site using a methodical risk-mapping process.
This consisted of mapping 10 risks, each of which were evaluated in terms of the dangers involved and the importance of the risk.
Combining this with the number of people involved, and the seriousness of potential outcomes, produced a probability–consequence risk rating for each activity.
Higher ratings required an additional round of assessment, with an operational analysis conducted by a health, safety and environment team.
This led to the definition of special procedures for specific risks, such as electrical work, work in confined spaces and work at height.
Unified system facilitates health, safety and environmental management
SAE, CCSA and all contractors were required to use a unified system (SSTMA) to manage occupational safety risks. The system is guided by a policy document and described in a fully detailed manual.
It covers aspects such as, but not limited to: legal documentation; risk assessment and management; sanitary conditions; preventive health care; personal protective equipment (PPE); accident prevention; work at height; work in confined spaces; work with electricity; safety signage; blasting; emergency procedures; training; safety inspections; and investigations of accidents. Safety themes for the day were discussed at morning meetings each day.
Human resources managers provide multiple levels of oversight
SAE’s and CSAC’s special purpose human resources and HSE staff monitored the application of systems and the emergence of issues.
Each employee was given four hours of initial training and a set of performance criteria to be evaluated on a monthly basis."
They analysed trends in accident and turnover rates, and identified opportunities on other projects for demobilised workers.
A range of organisations were involved in auditing personnel and safety practices: government bodies, i.e. the national electrical energy agency (ANEEL), the Ministry of Labour and the regional superintendent for labour; an independent auditor, as part of the SSTMA, every six months; and auditors assessing compliance with the IFC performance standards, appointed by financers.
Strict standards applied equally to all contractors and sub-contractors
SAE’s and CCSA’s safety standards were applied equally to all contractors and sub-contractors. Each new potential contractor was subject to a comprehensive risk analysis before contracting.
An initial meeting was held once the contract had been signed to conduct detailed analysis and definition of critical risk vectors for which management measures would be necessary.
Each employee was given four hours of initial training and a set of performance criteria to be evaluated on a monthly basis. Each contractor knew their employees’ results and areas for improvement. Workers had to show evidence that they had passed the safety training in order to gain access to the project site.
CSAC carried out monthly checks to ensure that contractors were conforming with their contractual obligations, using a system of 0–5 performance scores.
Workers’ commission provided regular forum for communications
There were three main channels through which workers could report any grievances:
the worker’s immediate supervisor;
- an anonymous ombudsman system, giving responses within a maximum of 48 hours; and
- a workers’ commission, i.e. a group of workers' representatives.
The commission coordinators met three times a week to discuss day-to-day issues, and any issues reported to line managers for immediate action. If this did not yield a satisfactory resolution, the issue would then be escalated to the next level. If still not resolved at that stage, it would then be raised to the CCSA ombudsman. The aim was to create good conditions for all workers.
Typical issues raised included workers' accommodation (e.g. quality of light, cleanliness of bathrooms), transport, interpersonal relationships and bureaucratic issues.
Every first Wednesday of the month, members of the workers' commission met company representatives including the HR department. This approach had a significant positive impact on communications, and on workers’ safety.
Variety of training opportunities fosters employee satisfaction
Workers were offered a number of different training opportunities, in areas such as: work safety; personal health; technical skills; health and safety courses related to the worker’s function; and technical courses appropriate to the worker's function.
Whenever a worker was promoted, they were offered 45 days of preliminary training, after which the promotion was either approved or rejected. Programmes for leadership were offered at all levels.
There were also special campaigns in areas such as sexual health, combating violence against women, and sexual abuse of minors and adolescents.
Loyalty incentives promote staff retention
Stiff competition for qualified workers in Brazil prompted the project to develop a special programme for labour retention.
The programme included benefits linked to a worker's period of employment, including salary increments after every six months of employment (up to 18 months).
The living and reacreational facilities provided to workers were also a major factor in employee satisfaction.
The project was careful to support workers in the demobilisation phase, offering an interview to evaluate performance and identify interests in other project opportunities.
This case study is based on an official assessment of Santo Antônio using the implementation stage tool of the Hydropower Sustainability Assessment Protocol. This was conducted in 2014, with an on-site assessment in April-May 2014.
The case study is featured in Better Hydro: Compendium of Case Studies 2017, which highlights examples of good practice in hydropower sustainability across all aspects of project development. You can download the full compendium here.